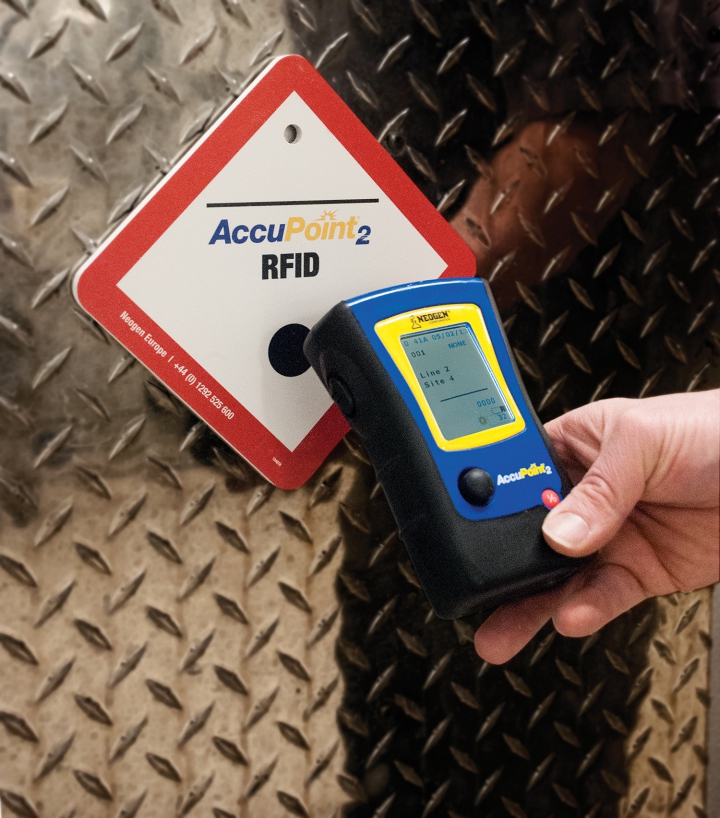
Neogen has introduced an advanced ATP hygiene monitoring system that uses radio frequency identification (RFID) technology to make testing in a facility much easier, and an updated software program to simplify data creation and interpretation.
Neogen’s AccuPoint® 2 Hygiene Monitoring System features the newest advancement in ATP monitoring, RFID technology. The technology involves two components: an antenna and RFID tags. The tags are passive, which means they give off no signal on their own. They simply reflect the RFID signal back to the instrument with their specific code, which is linked to the appropriate test site grouping. To keep from being a potential point of contamination, the RFID tags, which are about the size of a euro/pound coin, have been inserted into a 15 cm x 15 cm, brightly colored sign.
“We didn’t invent RFID technology,” said Neogen’s Rob Soule. “We simply took this terrific technology that’s been used in everything from inventory tracking to cattle identification to keyless applications access and figured out a way to automate some of the things that our customers were telling us take up too much of their time.”
The user simply swipes the instrument near the tag and the site group is read automatically. From there, the instrument picks test sites within the site group automatically at random. And if the facility has chosen to designate some test sites as mandatory, meaning they are “hot spots” or sites that need to be tested each time, those are presented first and appear in red on the instrument’s display.
“The RFID technology is the ‘wow’ factor of the newest ATP systems. We’ve tried to move the design of the day’s test plan from the manager’s computer to the instrument,” said Soule. “In the past, you would have to create a daily test plan on a computer and upload it to the instrument, then toggle and scroll, and toggle and scroll some more to get to the appropriate test site before you could test the site — for every site you tested. We’ve eliminated all that. With just one swipe the instrument can be ready to test.”
A daily test plan can be developed to monitor the effectiveness of the facility’s cleaning program by testing any or all of the points. Because most facilities have more critical control points than can be realistically tested on a daily basis, in the past supervisors had no other choice but to take the time to attempt to tailor daily test plans to best ensure the overall cleanliness of the facility.
With today’s ATP monitoring systems, all a supervisor has to do is identify test sites just once as either being mandatory, meaning they are tested every day, or as being of lower risk, which means the sites are among those that are tested on a random basis. With this information, a test plan can be automatically created on a daily basis - completely eliminating the supervisor’s once daily responsibility.
Not only have the latest ATP monitoring systems greatly improved upon the creation of test plans and the actual testing, but the analyzing of the collected data has seen numerous advancements since ATP technology was first used.
“We are in the information age and it’s really about how or what we do with the information that is important. Whether that information is used to comply with the seemingly endless global food safety regulatory initiatives, or simply finding a way to better produce your products,” said Soule. “The goal is to make sense of the data that is collected. Data collected through an ATP program is meaningless unless it can be interpreted, and used to help modify cleaning programs to produce unerringly effective results — the ultimate goal of hygiene efforts.”
The newest ATP monitoring systems can easily produce results that display:
- Results by test sites
- Results by test site groups
- Results ranked by highest percentage of fails
- Results by date ranges
- Trends by monthly averages
AccuPoint with RFID technology will revolutionise your hygiene monitoring process by removing paperwork both on the factory floor and in report building. It will reduce staff training and improve your process by prioritising areas that are deemed mandatory for testing. It will also highlight to your customers or prospective partners that you are serious about your hygiene monitoring.