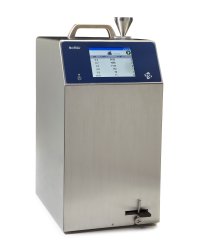
Introduction
FDA Guidance on Aseptic Processing 2004 and EU GMP Annex 1:2008 details the regulatory expectation to minimize the risk of microbiological, particulate and pyrogen contamination. Emphasis is placed on risk reduction and a proactive process focused Quality Assurance approach, rather than reactive product based Quality Control methods. The goal is to prevent contamination of products during aseptic processing, not identify contaminated or defective product at the end of the process.
The Measurement Challenge
Aerosol sampling instruments such as Active Air Samplers (AAS) and Optical Particle Counters (OPC) face a challenge of sampling relatively small volumes of air, compared with the total volume of air passing through a critical clean zone. This challenge is compounded in the case of an AAS when configured to sample infrequently.
Limitations of traditional growth based detection methods means that efficiently capturing an airborne particle carrying microbiological contamination and the subsequent successful growth of a visible colony is challenging. As a result, zero recovery from an AAS in the Grade A /ISO 5 zone does not automatically mean that the process environment is free from any microbiological contamination.
When there is microbiological recovery, investigating the root cause is extremely difficult, time consuming and oftentimes inconclusive. Understanding how the microbiological contamination arrived in the Grade A /ISO 5 zone is vital. It certainly does not magically appear. There will have been a transfer mechanism, a pathway through from the outside world via EU Grade D, Grade C / ISO 8 then Grade B / ISO 7 finally arriving in the Grade A / ISO 5 zone.
Prevent Contamination
A proactive approach is to prevent the contamination event from occurring in the first place.
Very clean Grade A / ISO 5 processes continue to be interrupted, possibly unnecessarily. Even when barrier technology is deployed, growth media is introduced and manipulated to meet the regulatory expectation to perform environmental monitoring. The exciting prospect exists that these potentially risky and disruptive interventions are no longer necessary.
Real-time airborne viable particle counters can continuously monitor multiple critical locations in Grade A / ISO 5 processes as part of a contamination risk reduction strategy. This Rapid Microbiological Method (RMM) uses Laser Induced Fluorescence (LIF). Each particle is individually analyzed in real-time to determine viability. In the case of TSI’s BioTrak® Real-Time Viable Particle Counter, it samples continuously at a sample flow rate of 28.3 LPM or 1 CFM and easily integrates into TSI’s FMS Facility Monitoring Software.
Operators will know immediately if there is an airborne microbiological excursion, enabling a real-time response to a contamination event. Responses can include halting the process to prevent any further contamination risk to product, containers or closures.
Predict Contamination
Another proactive approach is to predict a contamination event, rather than a reactive approach of waiting for a contamination event to occur.
Predicting contamination events in the Grade A / ISO 5 zone may seem more challenging. Environmental monitoring is performed intensively in the cleanest areas where barrier technology effectively segregates operators from critical process. Here the frequency of airborne microbiological recovery events is very low.
In isolation, data from the Grade A /ISO 5 zone does not represent a complete picture of a facility. Changes in the environment in key locations surrounding the Grade A / ISO 5 zone may be a warning of a potential contamination event.1
Grade C /ISO 8 or Grade D supporting areas are specified in aseptic processing guidance to have measurable microbiological and total particulate levels. Targeted risk based monitoring in key locations in these areas, where microbiological contamination can be transferred, builds a complete picture of the contamination present within the facility. Any changes in microbiological flora and recovery rates in these key locations could mean an increased contamination risk to the critical Grade A /ISO 5 zone.
A real-time viable particle counter will immediately detect changes in environmental air quality indicating an increased risk to the aseptic core. Predicting the possibility of a contamination event leads to proactive steps that can be taken to prevent microbiological contamination reaching the critical Grade A /ISO 5 zone.
Conclusion
Detecting changes in levels of airborne microbiological contamination in real time in all areas of a life science manufacturing facility is now a reality. Instruments such as TSI’s BioTrak Real-Time Viable Particle Counter facilitate proactive Quality Assurance based approaches. They detect airborne viable particles in real-time, and per the current EU and US FDA aseptic processing guidance, monitor total particle counts simultaneously, via a single particle monitoring probe. All optically analyzed particles are collected on a filter to facilitate laboratory analysis using and traditional growth based methods or an alternate rapid method.
LIF-based, real-time airborne viable particle counters can be deployed as part of a contamination risk reduction strategy. The focus is proactively understanding a facility and preventing microbiological contamination from reaching critical manufacturing areas.
- 1. PHSS Bio-Contamination Monograph 20, Bio-contamination characterization, control, monitoring and deviation management in controlled / GMP classified areas