Biofilms are fascinating, but to manufacturers, they are potentially dangerous communities of microorganisms that band together to form a slimy, resilient fortress on various surfaces. Like a microbial metropolis, they are teeming with bacteria, fungi, and yeasts encased in protective polysaccharides enabling them to withstand extreme processing conditions and cleaning cycles and generally evade the best efforts to eliminate them.
From the spotless surfaces of food processing equipment to the intricate pipework of water treatment facilities, biofilms can take root and flourish, often undetected, until they cause serious problems such as equipment fouling, corrosion, and contamination, significantly affecting processing efficiency and product quality. Accurately identifying the presence of biofilms is crucial for taking effective remedial action.
EIT International's new BactiScan™ revolutionises biofilm detection in everyday production settings, offering a groundbreaking solution for manufacturers. Here, we explore with Mariza Fraser, Global Sales Manager, EIT International, the remarkable capabilities of this innovative tool and discover why it's becoming the go-to solution for industries battling with biofilms.
Q: What challenges do biofilms pose in production settings?
Mariza: Biofilms can spread across all surfaces, including ceilings, walls, and floors. Many production facilities focus only on visible areas where food is handled, mistakenly believing that sanitizing these spaces alone prevents contamination. Since biofilms are invisible to the naked eye, this approach leaves other areas at risk. Bactiscan technology reveals hidden biofilms, enabling more precise targeting during sanitation. This not only ensures a thorough cleaning but also helps organizations evaluate the effectiveness of their cleaning regimes, improving overall hygiene.What is the traditional approach to biofilm detection?
Q: How is the Bactiscan different? What sets it apart from a traditional UV light?
Mariza: Traditional UV lights operate on a single wavelength, reflecting off certain invisible materials but often missing biofilms. In contrast, Bactiscan uses four distinct frequencies to “excite” biofilms, causing them to glow and making them easy to differentiate from other contaminants. This multi-frequency approach provides a more accurate identification of biofilms, enabling more effective cleaning and targeted sanitation efforts.
Q: How versatile is the Bactiscan? Are there any scenarios where it wouldn’t be suitable?
Mariza: The Bactiscan can be applied directly to all surfaces, effectively revealing biofilms through the excitation of bacteria by its four UV wavelengths. However, it cannot penetrate barriers such as glass or water, as these materials distort the UV light, preventing it from reaching the biofilm. This limitation makes detection and access to the biofilm challenging in such cases.
Q: Which sectors are finding Bactiscan to be a game-changer for their operations?
Mariza: Bactiscan is utilized across various sectors for both sanitation and research and development. The BactiscanPro is particularly effective in Quality Assurance, where production facilities implement it as a best practice to demonstrate their high standards of sanitation to consumers. Additionally, it serves as a valuable tool for training purposes and in the research and development of cleaning products, ensuring their effectiveness.
Q: Walk us through the process of integrating Bactiscan into a facility's routine. Any tips for a smooth transition?
Mariza: To integrate Bactiscan into a facility's routine, start with a comprehensive assessment by mapping the entire facility to identify key areas needing attention, from reception to production zones. Use Bactiscan technology to scan surfaces, detecting hidden biofilms and contamination
Q: How do companies transform the Bactiscan results into actionable data?
Mariza: To integrate Bactiscan into a facility's routine, we recommend starting with a comprehensive facility mapping process. This involves assessing areas from reception to production, using Bactiscan to identify contamination hotspots. Once these areas are highlighted, a Standard Operating Procedure (SOP) should be created, outlining cleaning processes and appropriate products to address contamination. Training staff on these new procedures is essential for successful implementation. For a smooth transition, engage key stakeholders, consider piloting in smaller sections, and monitor the effectiveness of the SOP for continuous improvement.
Q: Can you share a real-world example where Bactiscan uncovered issues that other methods missed? What was the impact?
Mariza: We recently visited a children's hospital in Buenos Aires, Argentina, where we discovered a troubling issue in one of their operating theaters: patients were leaving with infections. Upon scanning the room, we identified significant biofilm growth next to an air vent blowing air into the space, which was splattered with contamination. While the beds, lights, and equipment were sanitized, the floors were covered in cleaning product residue, creating a serious contamination risk that was contributing to the bacterial infections in patients as well.
Are you ready to revolutionise your biofilm detection process? To get your free demo, use the request info button below.
About Mariza Frazer
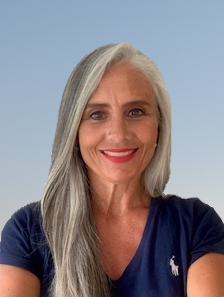