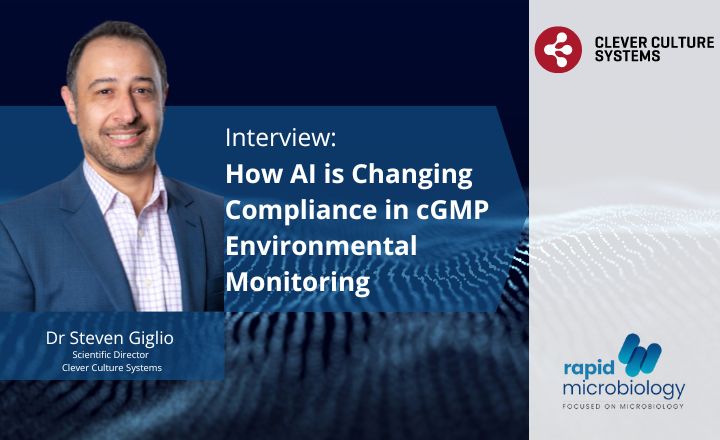
How AI is Changing Compliance in cGMP Environmental Monitoring
Key Points
- ready to use specially packaged media are available for environmental monitoring
- trending of monitoring data helps set action and alert levels
- pinpointing contamination sources is vital
A clean room is an environment where the levels of airborne contaminants are controlled to conform to specifications detailing the number, nature and size of the permitted particles. The air drawn into a clean room area is filtered and re-circulated through HEPA filters to control the level of particulates. Designation criteria, measured in particles of designated size, per volume of air are well established and are formalized in ISO 14644. Other classification systems, e.g. US Federal Standard 209E, are still in use and the systems are comparable at the 0.5 µm particle size.
The ISO 14644 standard assigns classification as a function of the logarithm of the maximum number of permitted particles, 0.1 µm or larger per cubic metre of air, e.g. 1000 particles >0.1µm per m3 = ISO 3. The US federal standard 209E assigns classification as a function of the actual number of particles, 0.5µm, per cubic foot of air, e.g. 1000 particles, 0.5 µm, per ft3 = Class 1000. The smaller the number the more controlled the environment.
Clean rooms are utilized in a variety of industry sectors including electronics, pharmaceutical and biotechnology where production processes are highly sensitive to both physical and biological particulate contamination. They vary in size from entire manufacturing areas to small workstations often termed isolators. Whereas no distinction is made by any classification system as to the nature of the particle, it is generally accepted that where fewer airborne particulates exist in a controlled environment, the less likely it is that micro-organisms will be present.
Classification does not require data that distinguishes between physical and biological particles, however regulatory conformance will. Monitoring the controlled environment for particles of a given size will not directly report the microbiological status. Micro-organisms will associate with physical particulates and therefore it is necessary to include monitoring techniques that satisfy both the classification and regulatory requirements by differentiating the microbiological component of a test.
Regulation It is critical to the performance of clean room environments that a properly designed and implemented monitoring program is applied. The selection of sampling sites, number of locations and frequency are described in various official documentation, e.g. ISO 14644, ISO 14698 and USP Chapter 1116.
The selection of methods, media and incubation are also detailed in ISO 14698, PDA TR13 and USP Chapter 1116. The USP chapters 1208 and 797 also deal with aspects relating specifically to isolators. Sampling plans should not be fixed. As performance data relating to specific environments builds, modifications to the sampling plan should occur to reflect increases or decreases in the number of sites and frequency of testing.
Monitoring
It is accepted that the presence of micro-organisms in a controlled production environment can affect the quality of the finished product or process intermediate.
Guidelines are set that specify the maximum number of colony forming units (cfu) for a given volume of air or on a surface. At the very highly controlled end of the spectrum, e.g. Class 100 clean rooms, the level of contamination is 3 cfu per volume/surface. Microbiologically this presents a challenge as statistically the data at this level will have relatively high standard deviations. The setting of action and alert levels in clean room environments should account for this and allow for trending of data over time rather than respond to a single out of specification (OOS) result.
The areas generally monitored in a clean room environment include personnel, ventilation, building fabric and equipment. Both the airborne and surface contamination levels are tested. Testing should take place with the clean room in operation, however baseline data from cleaning validations and 'as built' conditions should also be collected.
Viable airborne contamination can be monitored passively using settle plates (usually TSA for a bacterial count and SDA for yeasts and moulds). Here the number of microbial particles falling or settling on the surface of an opened Petri dish within a given time is assessed. This technique is most often used in areas of little air movement. Active air monitoring is also used to assess the viable particles in a fixed volume of air within the clean room. This technique can also monitor contamination in compressed gases. The technique utilizes a forced volume of air passing over a growth medium that is subsequently removed from the instrument and incubated. There are many variations to this theme that are covered in USP Chapter 1116.
Clean room surfaces are monitored either by a swabbing technique or by contact (Replicate Organism Detection and Counting or RODAC) plates. Monitored surfaces should include personnel protective equipment (PPE), walls, floors and equipment. Swabbing has a reputation of giving a poor rate of recovery although there is the advantage that no media residue is left on the tested surface. After incubation, results from contact plates can be used to calculate the cfu per unit area. Choice of media in the contact plate depends on the environment, the perceived microbiololgical risks and the preference of the individual microbiologist. If a surface has been disinfected then the plate media needs to contain one or more appropriate neutralizing agents, common ones used are Lecithin and Tween (Polysorbate) or Thiosulphate, L-Histidine, Thioglycollate and bisulphate in various combinations. If the area is being used for antibiotic production then the media will also need to contain a suitable inhibitor (eg a beta lactamase for a Cephalosporin product).
Commercial media intended for use in a clean room are irradiated to ensure contaminated plates are not accidentally bought in and that the packaging itself is not a contamination source. These are available, double or triple wrapped in Vapour-phase Hydrogen Peroxide (VHP) impermeable packaging which protects the media from commonly used sterilzation vapours so keeping the media in optimum condition for recovery and growth of contaminants.
Data generated by microbiological testing, at the levels specified, should be monitored for trends with alert and action levels designed to allow trends to form before critical action is taken. Identification of isolated organisms is useful in understanding and responding to OOS results, in evaluating cleaning regimes and investigating sources of contamination. An environmental monitoring program cannot detect all events that may compromise the quality of the product or process but should be capable of detecting a drift in the microbiological status of the environment that will allow intervention to rectify the problem. Periodic process simulation studies or media fill trials will also help to ensure that operating conditions are in control.
Comments
Most recent developments are in the areas of:
- improved media quality and presentation
- data collection and analysis
- complete automation of plate reading and reporting using AI based software
- molecular identification methods designed to better highlight sources of contamination
Get the latest updates in Rapid Microbiological Test Methods sent to your email? Subscribe to the free rapidmicrobiology eNewsletter